Catalytic reforming plays a crucial role in refineries worldwide. This article will delve into its basic process, main equipment, and functions, including hydrogenation reactors, fixed-bed reactors, moving-bed reactors, oil-gas separators, dehydration towers, and stabilization towers. It will also explain how these components work together to ensure the efficient and stable operation of the catalytic reformation, enabling effective conversion of petroleum resources and production of fine chemicals.
Main output 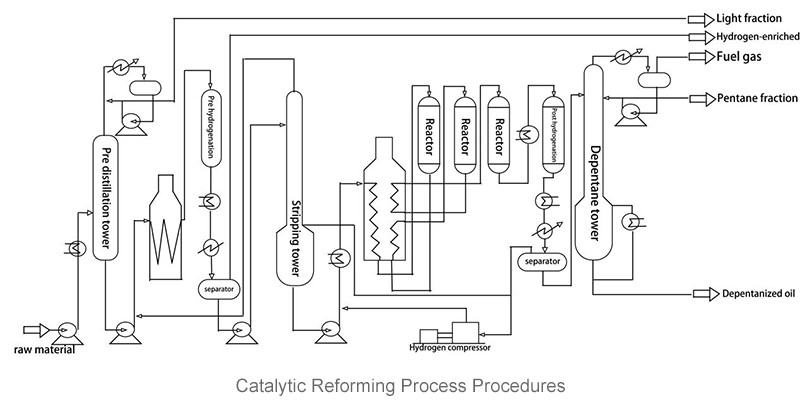
(1)C6-C9 aromatics;
(2)high-octane gasoline(reforming oil);
(3)benzene, toluene, xylene(extracted by aromatics)
By-product
Hydrogen(input of hydro-cracking and hydro-fining)
Input includes light gasoline fraction (or naphtha) from crude oil distillation,which requires pretreatment:pre-dearsenification, pre-distillation, pre-hydrogenation. Next, catalytic reformation will rearrange hydrocarbon molecules into a new molecular structure.
Main Equipments in Catalytic Reforming Process
Hydrogenation Reactor
1.In a catalytic reforming unit, the hydrogenation reactor is usually in the pretreatment stage. Its main function is to hydrotreat the raw material to remove impurities in the raw material, such as sulfur, nitrogen, oxygen and metal impurities. These impurities can have a toxic effect on the subsequent reforming catalyst, resulting in catalyst deactivation. For example, sulfur binds to the active centers of noble metals in reforming catalysts, such as platinum, rendering them inactive. With the hydrogenation reactor, the sulfides in the feedstock can be converted to hydrogen sulfide, which can then be removed through the subsequent separation process, thus protecting the reforming catalyst and extending its service life.
2.The hydrogenation reactor can also hydrosaturate the unsaturated hydrocarbons in the raw material to reduce the occurrence of side reactions such as olefin polymerization in the reforming process. Because olefins are prone to polymerization under reforming conditions, colloids and coke are formed, which can clog the pores of the catalyst and affect the normal progress of the reaction.
Fixed-bed Reforming Reactor
This is the most common type of reforming reactor. It consists of one or more fixed catalyst beds. The feedstock oil reacts through a catalyst bed from top to bottom (or bottom up). Its advantages are simple structure, stable operation, and the catalyst is not easy to lose. For example, in a semi-regenerative catalytic reforming unit, a fixed-bed reactor is usually used, and its catalyst can be regenerated after a certain operating cycle.
Moving Bed Reforming Reactor
This type of reactor is characterized by the fact that the catalyst can move slowly in the reactor. As the reaction progresses, the deactivated catalyst is gradually removed from the reactor for regeneration, while new or regenerated catalysts are constantly replenished. The moving bed reactor can continuously carry out the reaction and catalyst regeneration to ensure that the reaction is always carried out in the ideal catalyst activity state, which is suitable for large-scale and continuous reforming production process, such as continuous reforming units are widely used in moving bed reactors.
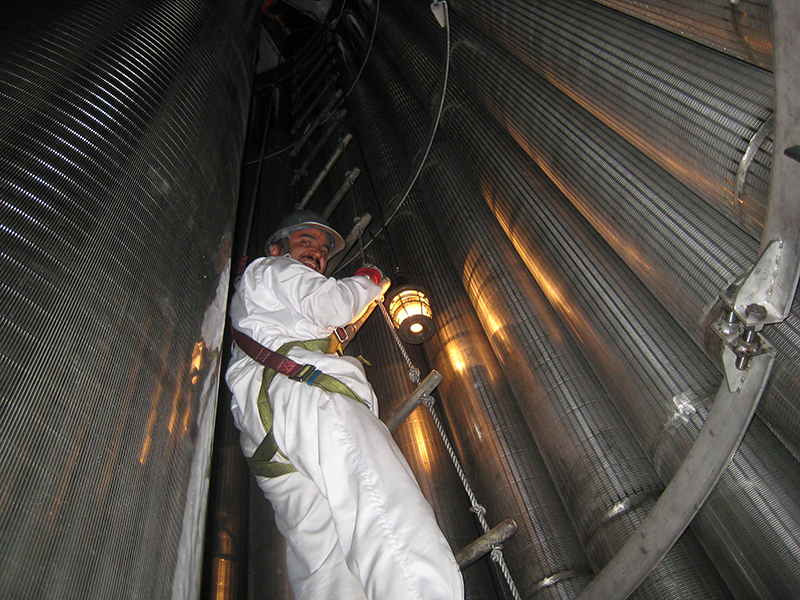
Oil-Gas Separator
In the catalytic reforming process, the oil-gas separator is mainly used to separate the gas and liquid phases in the reaction products. The product of the reforming reaction is an oil-gas mixture, which contains hydrogen, gaseous hydrocarbons, and liquid gasoline and aromatic hydrocarbons. They are separated by an oil-air separator so that the products of the different phases can be processed separately at a later date. For example, the separated hydrogen can be used in other petrochemical processes such as hydrorefining, while liquid products can be further processed, such as by fractional distillation to separate aromatic and high-octane gasoline components in different boiling point ranges
Dehydration Towers
Its core function is to remove water from the reforming product. Because the product of the reforming reaction contains a small amount of water, this water will adversely affect the subsequent aromatic extraction, product storage and transportation and other processes, such as affecting the aromatic extraction efficiency, leading to product deterioration and corrosion. Therefore, the dewatering tower focuses on separating the impurity component of water and reducing the moisture content of the product to the required level.
Stabilization Towers
It is mainly used to stabilize the vapor pressure of reformed gasoline by separating light hydrocarbon components such as C4 and lighter components in reforming products. If the vapor pressure of reformed gasoline is too high, excessive volatile gases will be generated during storage and use, resulting in product loss and safety hazards. The purpose of the stabilization tower is to ensure that the reformed gasoline meets the appropriate vapor pressure standards and to improve product quality.
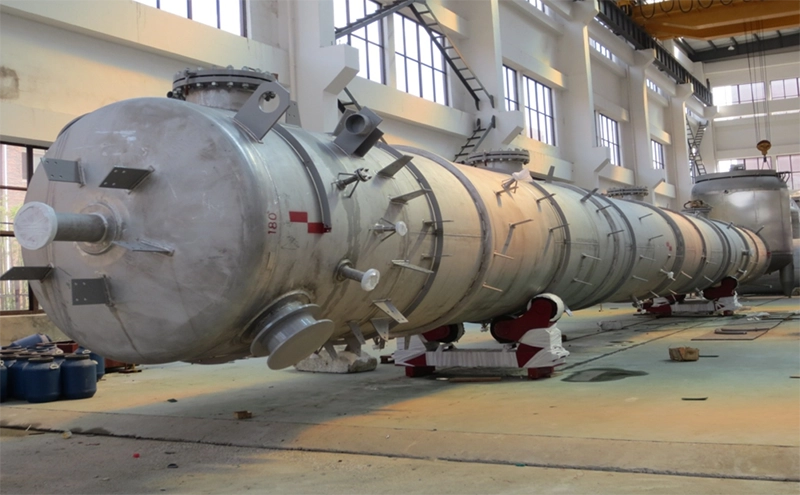